Not known Facts About Indonesia Furniture Manufacturers
Table of ContentsThe Best Strategy To Use For Indonesia Furniture ManufacturersIndonesia Furniture Manufacturers Things To Know Before You Get ThisNot known Incorrect Statements About Indonesia Furniture Manufacturers Excitement About Indonesia Furniture Manufacturers5 Simple Techniques For Indonesia Furniture Manufacturers
There are some downsides to buying from a furnishings manufacturer. For one, you may need to wait longer to obtain your furnishings because it's being made to purchase. Furthermore, you may not be able to see or touch the product before you buy it. A furniture retailer is a business that offers furniture made by various producers.When you purchase from a furniture merchant, you're getting a furniture piece that's currently been made and is all set to be shipped to your home. Among the advantages of purchasing from a furniture retailer is that you can often see and touch the product prior to you purchase it.
At BH Furniture, our company believe in setting brand-new requirements for excellence in the manufacturing of business furnishings - Indonesia furniture manufacturers. Our commitment to advancement has led us to embrace cutting-edge automation modern technology, changing the method we manufacture furnishings and driving us to the leading edge of the market. Gone are the days of manual work dominating the manufacturing floor
Claim goodbye to production hold-ups and overtime prices. This means we not only fulfill however exceed delivery due dates, supplying our customers with a degree of dependability that typical manufacturing approaches simply can't match.
All about Indonesia Furniture Manufacturers
Our manufacturing ability has soared, enabling us to satisfy the demands of also the largest jobs without jeopardizing on top quality. As your partner in industrial furnishings options, we can effortlessly scale our output to suit your demands, regardless of the scale. While traditional manufacturing depends heavily on manual work, our automated systems have significantly lowered our reliance on a large labor force.
Furniture production is a complicated procedure that includes various phases, from creating and material selection to manufacturing and assembly. At each phase, there is an opportunity of defects or errors that can jeopardize the quality of the end product. To make certain that furniture is of excellent quality, furniture suppliers execute quality assurance processes to recognize and correct any problems that may develop during manufacturing.
The evaluation procedure should cover numerous aspects, such as setting up, coating, colour, style, packaging, labelling, and noting. By implementing a strenuous evaluation procedure, manufacturers can ensure their items meet the needed quality, safety and security, and longevity demands. They also supply the flexibility to resolve issues and make improvements prior to completing the end product.
The procedure begins with the resources examination to the final setting up of the furniture. The objective is to ensure that the products are devoid of problems, safe, and satisfy the consumer's assumptions. Furnishings high quality standards are sets of standards and demands for furniture production. They specify the needed high quality level of furniture production and cover elements such as security, resilience, stamina, and ecological effect.
6 Simple Techniques For Indonesia Furniture Manufacturers

To ensure their furnishings items can endure different weather condition components, including sun, rain, snow, read what he said and wind, makers should take into consideration globally acknowledged requirements that consist of assessments and testing. Below are a few of the requirements to maintain in mind: ASTM F1561-03 is a global basic established by the American Section of the International Association for Screening Products (ASTM).
UL 962 is a global safety standard developed by Underwriters Laboratories (UL), an independent international supply security remedies business. The standard applies to family and commercial furnishings, including outside furniture.
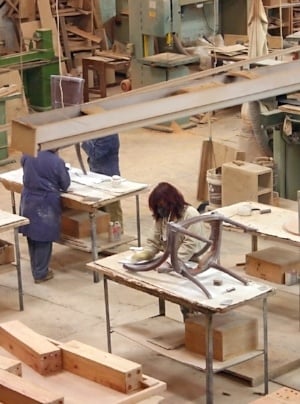
See This Report on Indonesia Furniture Manufacturers
It helps to determine defects in the furniture continue reading this and assess its efficiency and compliance with the needed top quality criteria. Right here are the steps for carrying out lab screening for furniture: Suppliers gather examples of furnishings elements that need testing. These examples commonly represent the various sorts of furniture that they generate.
This may entail a combination of various examinations, consisting of strength screening, durability screening, safety and security screening, and environmental effect testing. The samples are then evaluated for numerous high quality criteria, such as stamina, longevity, security, and ecological effect. The outcomes are then assessed to establish whether the items fulfill the needed quality standards.
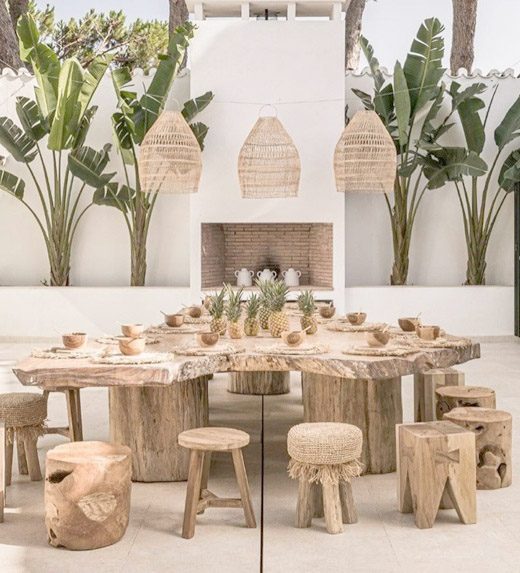
Usually, every store furniture is various. But all tasks have regarding a month's time between layout ideation and last manufacturing. This is where the major challenge lies. Layouts meeting client convenience Taking full advantage of space usage in storage, display, step, guest seating and walkways Making certain convenience of access to products for tests and acquisition Creating modular furnishings that is easy to move and refit Satisfying security demands of clients A fast TAT from design to production and installation with very little errors can help attend to the above problems.
Indonesia Furniture Manufacturers for Dummies
Also, a developer can comprehend the market patterns and prepare with innovative designs beforehand. Check out here: How DriveWorks Assists You to Minimize Preparation in Manufacturing Developers typically need to alter the sizes and shapes of furniture at a minute's notice. These might have various aesthetic and functional needs like front desk, and maintenance desk that differ in dimensions.
Enhances index item quality and reduces scrap. Area direction documents along with quantity departures are likewise created for retail shop furnishings installments. Design iterations and conflicts are decreased, and the shop flooring can start producing on the day of sales.
It is a very affordable market, with organizations aiming to maintain up with changing consumer demands and the latest technological trends. Today's customers are more likely to prefer furniture that is customized and made with sustainable materials.